When we have two 3D printed parts that need to fit together, many of us rely on pins and holes to locate them and fix them together. [Slant 3D] has explored some alternative ideas in this area that may open up new avenues for your own designs.
Their first idea was to simply chamfer the pins and holes. This allows the object to be printed in a different orientations without compromising the fit. It also makes the features less brittle and creates a broader surface for gluing. Another alternative is using fins and slots, which again add robustness compared to flimsy pins. By chamfering the edges of the fins, they can be printed vertically for good strength and easy location without the need for support material. Linch Pin
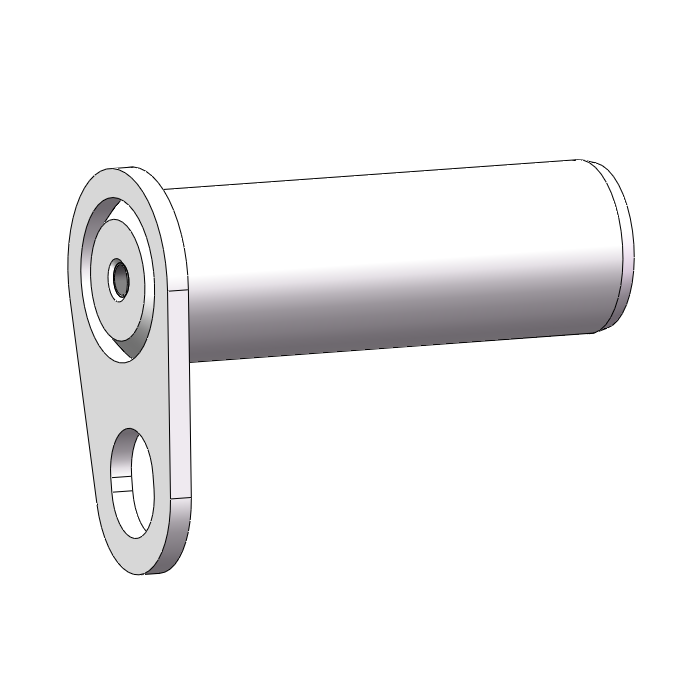
Neither option requires much extra fuss compared to typical pin-and-hole designs. Plus, both are far less likely to snap off and ruin your day. Be honest, we’ve all been there. Meanwhile, consider adding folded techniques to your repertoire, too.
I personally prefer nesting-type location features like gridfinity containers use.
It’s probably a lot stronger then pin, a way to be self align is the have them one in each axis. Or a cross this way it’s centered
I thought of the cross too. With clips so that it stays in place.
This seems to me to be a sort of reinvention of kelvin and maxwell kinematic joints. Particularly maxwell couplings, using three linear concave curved surfaces and three convex hemispheres, that guarantee positional accuracy in a way that’s pretty easy to make with a 3d printer.
In the woodworking world they’re called biscuits…
I was just coming to say that too. I never used them but norm abrams loved them.
He backed off when he found out that over time dimples formed on the surfaces above the biscuits.
For my plaster of paris mold masters I’ve found that there are numerous alignment possibilites; what’s most critical for my needs is figuring out what it’s going to take to release the plaster from the plastic master mold AND yield plaster molds (in multi-part molds) which can easily fit together as well as last through dozens or castings with the clay castig slip used for the creation of the final piece. Sharp angles need to be fillited or chamfered and draft angles are also critial for a plastic master that will yield a set of plaster molds which can seamlessly fit together AND allow for a smooth release. Similar to 3D printed articulating parts, the plastic masters need to allow for 0.1 – 0.3mm clearances in the final casts. The 3D CAD designed “perfect” fits won’t fit in the real world…
The techniques for making plaster slip casting molds translate very well to fiberglass molds, and to silicone molds. I’ve done all of those. Do you have Thurston James’ books?
Thanks for the book(s) suggestion; If I were still dabbling in theatre I can see their value. My two go-to resources are Frith’s Mold Making for Ceramics, and Andrew Martin’s The Essential Guide to Mold Making & Slip Casting. I am more focused on ceramics and functional pottery (mugs, plates, bowls, vases, etc.). The very short version, I hate messing with cottle boards, so one aspect of what I do is to 3D print custom cottles for each project. It does add time, but saves my sanity and avoids all the frustrations with making chamfers and dealing with all the various ways plaster can find a path out of the mold and on to my table and floor… :)
seems like the alignment of a fin is a huge issue, even in the video he cant line up top of the model .
I just skipped through the vid, but it was painful to watch! You simply can’t reliably align two parts with 4 pins which go into 4 holes. Same thing with those fins!
It’s overconstrained. If you use just twi pins/holes it often works fine with 3D printing, especially if you have your printer well calibrated.
If you use one or more slots instead of a simple round hole the pins can self-align and move a tiny amount.
That a great idea. Just print the part with the slots twice and print biscuits separately.
Exactly. This vídeo is useless bs.
Indeed. I print 2 slots at 90 degrees, then I use scrap plastic sheet as biscuits. With orthogonal slots, the biscuit length has no effect. A similar trick is to use ovalled or pilled holes (with the oval direction at 90 degrees) and round pegs (e.g. nails, wire, filament). These techniques allow the parts to still mate when there is some size/scale mismatch across the part – a bit of problem with simple printers.
A little bit of draft angle for pins and fins is a good policy – about 2-3 degrees allows initial alignment, lets the parts slide into each other well without premature binding, and lets them seat firmly when things get all the way home.
Registration? Overconstraining? Tolerance? Diamond pins. Just sayin’. Like-magic alignment, no fuss. Chamfer as needed to suit printing requirements.
I recently said that we are doomed. There is so much basic knowledge out there. Books written about that stuff for centuries. I personally had the joy to hear lectures about such stuff. It was/is fantastic.
And then we are here, looking at a youtube video where it all starts from scratch.
At least AvE is some light in the darkness.
Diamond pin in round hole, and round pin in slot ftw. It’s like people never heard of kinematic mounting systems. 3 point contact or pins as described about are most constraining with least over constrained assembly conditions.
Those are solutions to a different problem. Kinematic couplings are for two separable items that need to repeatably align when mated with fairly low force holding the two together (i.e. alignment is more important than load-bearing). Here, the goal is a maximum strength glue-up joint, so maximising perpendicular surface area would be a better solution. Fins are not the best here, preferable would be a dovetail joint as long as it is possible to perform a slide-fit, otherwise a finger joint combined mechanical strength of the joining surface (the vulnerability of a thin fin) with high surface area, tuned by varying finger frequency across the surface.
Diamond pins are a good suggestion, but can be difficult to make with 3D printing, unless we’re talking about very large pins. If you make the pins separately you have issues with small-part bed adhesion and dimensional tolerances (because of elephant-footing), but if you integrate the pins into the part they’re either very fragile or require extra support, depending on orientation. And part orientation is already a headache in designing for print, so it’s good to avoid anything that constrains it further.
I’ve had a lot of success using short lengths of waste filament as pins, though – they take zero time to print, they’re isotropically strong, and the corresponding holes are small enough to print without support in any orientation. So there might be some value in using 1.75mm round pins with square holes.
i’ve just never wanted to do this. i almost always anchor things to eachother with holes for screws (or steel wire or nails or twine or hose clamps or …). i have always wanted to use a different material for the ‘biscuit’ part of the join. it just doesn’t make sense to accept the delamination properties of 3d printed plastic in a biscuit.
Hmm.. mixed feellings about this.
On one hand, it’s true that the maker of this video would benefit from reading an introduction to kinematics, then digging into the subject of minimum constraint design.
On the other hand, this happens when people learn a subject on their own. The idea that people should just absorb all the knowledge of a mechanical engineering degree is silly, and the idea of cutting people down for things they haven’t learned yet is toxic gatekeeping.
So let’s give partial credit: the video represents an early approach to an important subject. It will be a new idea to a lot of other people who are also picking things up on their own. Let’s those of us who’ve done some more reading try to encourage more learning:
“you’ve found an important subject and developed a couple of good ideas, but the material you’ve presented still has some flaws. The mature version of the subject is called ‘kinematics’, and the sub-topic of aligning objects to each other falls under the heading called ‘minimum constraint design’. The first major work on kinematics was a book called _The Constructor_ by Ruleaux, which is still worth reading today. Alexander Slocum from MIT has some excellent course notes available online:
http://pergatory.mit.edu/resources/FUNdaMENTALS.html
And Layton Carter Hayle’s PhD Thesis _ Principles and techniques for desiging precision machines_ is another excellent reference:
https://www.researchgate.net/publication/37606067_Principles_and_techniques_for_desiging_precision_machines
Take a look at those, and maybe make another video that reviews this one in terms of what you learn.”
Has someone done a nice ebook version of The Constructor, with the errata corrections swapped in where they say they should be? The scan of the book on Google Books is quite poor.
Your suggestions are great, but nobody on the Tube is going to take your advice. The big YouTube audience and money is in catering to the average viewer’s limbic system: doing things the average viewer can imagine themselves doing without a prior investment of time/effort/education. As much as we can dream, it’s not about education.
Consider a few selection criteria. Someone with a proper engineering education can make a stable full-time income in the industry. Someone who pursues a proper engineering education also might not be willing to stare at a camera for hours, edit videos, and constantly beg for subscriptions and likes. So – 999 times out of 1000, they avoid YouTube and go for the stable engineering income.
The very few highly-trained engineers on YouTube only do it part time. They get some views, but only when they voluntarily sacrifice quality for entertainment value.
So largely those doing engineering on YouTube are amateurs: naive engineers operating outside of their comfort zone, outside of the ‘best practices’ region. Software engineers will do mechanical engineering; biologists will make airplanes; high school graduates will do plasma physics; applied scientists will do EE; and so on.
Let’s do a subscriber comparison. AvE: 1.4M. Michael Reeves: 7M. Applied Science: 0.8M. Leo’s Bag of Tricks: 0.02M. w2aew: 0.2M. FliteTest: 2M. Simone Giertz: 2.7M. Hydraulic Press Channel: 5.4M. Peter Sripol: 2M. Waterjet Channel: 0.9M. Engineering Explained: 3.5M. EEVBlog: 0.9M. ElectroBOOM: 5.6M.
If you understand that YT is used as a substitute for experiencing reality, it begins to make sense why the most tedious and unoriginal (yet fresh and new) content performs well. Daily vlogs; video game playthroughs; worthless lifehack content; staged fights and outrage-inducing skits. They put you into a crib simulacra: your visual and auditory cortices are fully activated, your motor cortex is immobilized, new things are popping up all around your field of vision. That isn’t really the place to train yourself to make good decisions; and you certainly can’t do a problem set while one of those videos is playing.
There’s a reason every big YouTuber only plays montages of their CAD work in fast-forward. The vast majority, maybe 98%, of all viewers literally don’t care and will skip ahead themselves if a montage of 10 hours of CAD takes longer than 5 seconds to play. Or worse: unsubscribe and skip to another channel with more pop and pizazz.
The bitter lesson I’ve learned from YouTube is that the very highest quality engineering education videos — material that’s bone dry but backed up by decades or centuries of peer review — gets something like 1,000 views per decade.
To be clear: I don’t have anything against any of these people. They do what they have to to make an income just like anyone else.
i agree entirely and just want to go on a bit… youtube has a *lot* of content on it, and a lot of it is high quality even for an audience like myself. it’s just, that stuff isn’t lucrative. it doesn’t tend to surface in the search or recommendation functions.
it is really frustrating. sometimes i know i have already seen an expert give a competent demonstration of some technique, so i go back to view it again, and all i can find is a bunch of clickbait. people who don’t know anything about anything except assembling clickable videos. for example, i know there have to be ten thousand videos of people performing basic bicycle maintenance but the search function somehow just gives me 8 results, the rest is all “People also watched”. and the top 8 results are garbage. the thousands of less popular results are now unfindable??? i can’t believe it.
i don’t know all the mechanisms behind this phenomenon but there’s a lot of stuff that doesn’t fit this garbage mold, it’s just hard or impossible to find anymore.
I don’t have anything to add to the conversation but i have to say the quality of the comments here is absurdly high for an internet “forum”. Refreshing to see
It’s the same mechanism that puts dumpy snacks in your face at the supermarket checkout, unfortunately. Survival of the fittest as assessed by Google’s algorithm doing its best to perfectly match the viewers’ willingness to consume slop with their willingness to tolerate ads.
Mike Stone came up with some pretty great, constructive suggestions!
Man. I was in a cynical mood when I wrote this. My apologies, perusers of the comments!
“If you understand that YT is used as a substitute for experiencing reality, […]”
The apology below has been seen and noted, but I’d like to put a few points here for easy reference:
First I’d like to address the issue of false controversy: I stipulate that the number of people actively interested in 3D printing is smaller than the number currently discussing the atrocities against fabric perpetrated at last night’s Met Gala. My response is, “so what?”
I didn’t become a geek to have the scope of my interests dictated by the whim of the masses.
Tens of millions of people have no interest in Fourier transforms, yet am I well (I’m a Shakespearian too). I, in turn, decline to be interested in Lost, Twilight, Game of Thrones, or whatever the tidal surge of mass attention is flooding at the moment.
Second, and following on that, I’d like to address a fallacy of scale: If Dave Jones has something interesting to say, ‘only’ nine hundred thousand people are waiting to hear it. By the argument above, the only sensible response is a retreat into nihilistic despair.
I disagree. I consider nine hundred thousand people a subgroup large enough to be interesting. If the validity of interests has some numerical threshold, please define it. I’ll ignore the number continue to think H. Beam Piper, Cordwainer Smith, and the Hoka stories are awesome.
Finally, I’d like to address the notion of utility: the speech above deplores the status quo, rejects a suggestion on how to improve the status quo, and offers no better alternative. It’s a manifesto of cultivated impotence and resentment, objectively less useful than nothing at all.
I happen to be an old school geek, and stopped feeling the lash of normalization by open disapproval long ago. I do however feel a duty to beat this horse into the ground for the benefit of the younger geeks who might be intimidated into silence by a speech like the one above.
Toward that end, I’d like to refer to the old homily about “whenever there’s trouble, look for the people who are helping.”
To that I will add: “when you find them, at least *try* to resist the urge to kick them in the ‘nads.”
I gained nothing from writing my comment and only fed into negativity. I hope that it didn’t ruin anyone’s day.
Please be kind and respectful to help make the comments section excellent. (Comment Policy)
This site uses Akismet to reduce spam. Learn how your comment data is processed.
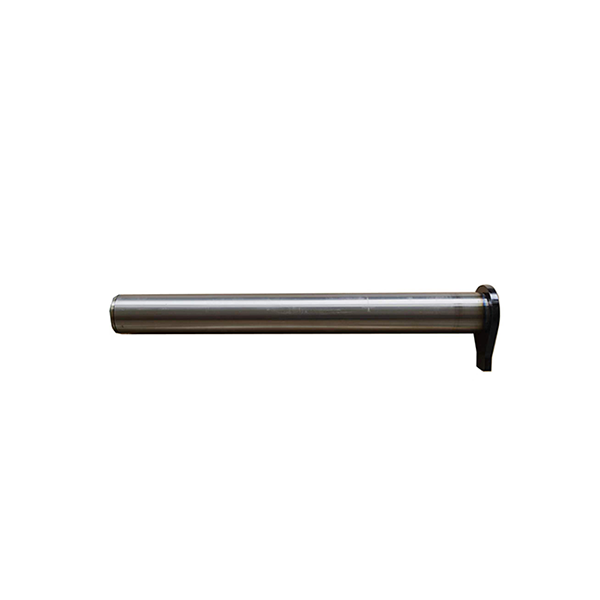
Digging Excavator By using our website and services, you expressly agree to the placement of our performance, functionality and advertising cookies. Learn more