The 51st annual SPE Automotive Innovation awards gave nods to several ‘firsts’ and added alternative vehicle systems category. #closeupontechnology
The all-electric 2023 Cadillac Lyriq and a team from GM, Detroit and its suppliers won the SPE Automotive Vehicle Engineering Team Award. (Photos: SPE Automotive Div.) Bulk Tpu Pellets
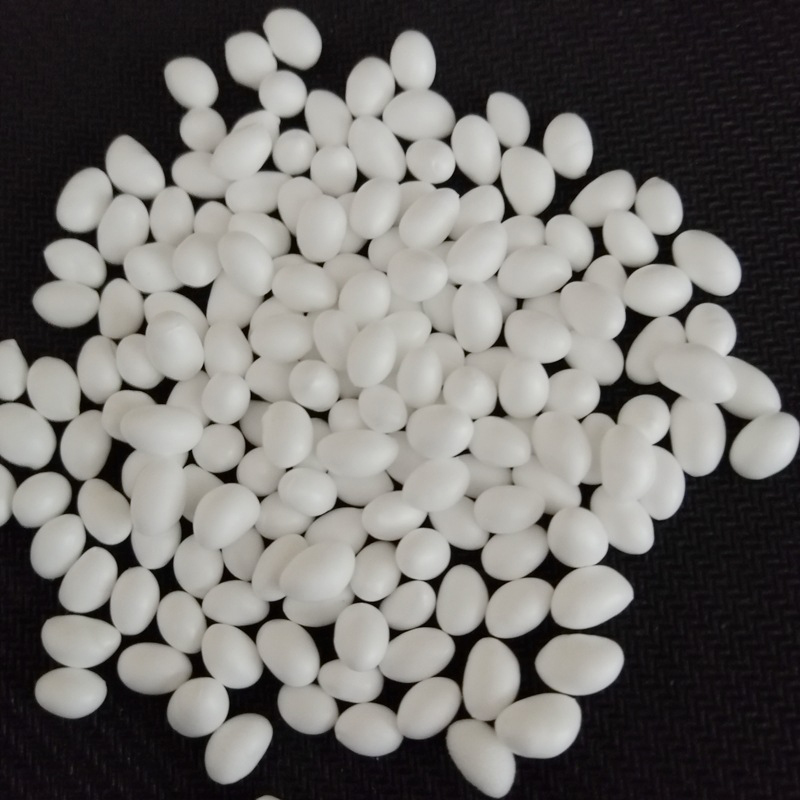
The 51st annual Society of Plastics Engineers Automotive Division Blue Ribbon Automotive Innovation Awards once again celebrated several “firsts” among 10 categories, which included innovations in the added categories of Electric & Autonomous Vehicle Systems and Aftermarket & Limited Edition/Specialty Vehicles and an expanded and renamed Sustainability environmental category. As has been the case for the last several years, thermoplastics led by far in all categories, though this year’s grand award winner went to a thermoset system in the winning Chassis/Hardware category, and other hybrid thermoplastic/thermoset processes were also included.
The 2022 Vehicle Engineering Team (VETA) award went to the team from General Motors Co. and its suppliers that developed the midsize all-electric 2023 Cadillac Lyriq SUV. This vehicle features numerous plastic and composite innovations, many of which were nominated in other categories of this latest competition, including Aftermarket & Limited Edition/Specialty Vehicles, Body Exterior, Body Interior, Electric & Autonomous Vehicle Systems, Materials, Process/Assembly/Enabling Technology, and Sustainability.
Now here’s a look at the other 2022 winners:
An industry first used a powder-bed fusion additive-manufacturing process to print 60,000 TPU spoiler closeout seals for the rear spoiler on the 2022 General Motors Chevrolet Tahoe, Chevrolet Suburban, Cadillac Escalade, and GMC Yukon. BASF’s SE Ultrasint TPU01 was used on the HP Multi Jet Fusion 5200 Series printer by tier supplier/processor AMT Ltd./GKN Additive (Forecast 3D) for 10 weeks of production as a bridge solution while hard tooling was being produced. It demonstrated the ability of additive manufacturing to achieve large-scale implementation. Innovative vapor polishing and drying processes were used to finish parts, eliminating the need for post-print dyeing and halving total production time.
Another industry first is the carbon-fiber/thermoplastic C-brace metal replacement on the 2022 Ford Motor Bronco Raptor. Injection molded by Montaplast of North America with BASF’s Ultramid B3 nylon 6 with glass and carbon fiber, this Class-A finish C-brace was designed to meet offroad desert durability requirements for convertible versions of the vehicle while boosting torsional stiffness by 40% to improve handling and NVH (noise, vibration, harshness). Weight was reduced by 55% vs. aluminum and 85% vs. steel by adopting a sandwich composite approach. The upper and lower shells were injection molded in the 35% glass-reinforced nylon 6 while a core was injection molded in 20% carbon fiber nylon 6, followed by bonding of the components with a newly formulated methacrylate adhesive.
Several novel technologies contributed to yet another first, the large injection molded, long-glass reinforced nylon 6 panoramic sunroof frame on the 2022 Hyundai Motor Group Kia Sorento. Manufactured by Inalfa Roof Systems Korea using GS Caltex’s Hiprene ALG14BF PA6, it is said to be the first of its kind made from flat rather than round glass fibers, which provided higher dimensional stability and reduced warpage. Also, twist pultrusion was used to produce LFT pellets whose fiber length exceeds the length of the pellets, again contributing to mechanical improvements. Weight was reduced by 51% vs. a steel frame and part count dropped from 33 to four. Versus carbon-fiber reinforced LFT, torsional rigidity was 13% higher and breaking force 25% better at 24% lower cost.
Another first, featured on the 2022 Toyota Motor Tundra, is the second-row seatback and cushion structure. It combines a pultruded continuous-glass reinforced PUR reinforcement beam, made from BASF’s Elastocoat 74850 80% GR-PUR, that is injection overmolded with BASF’s Ultramid B3ZG7 35% short-glass nylon 6. Produced by Flex-N-Gate Corp., Adient and L&L Products, it replaced a 60-piece steel-frame structure with a four-piece molded composite assembly. Over 100 welds at 16 weld stations were eliminated, significantly improving quality control. Significantly improved crash performance and 20% lower weight and cost were achieved, and the new version provides under-seat storage that wasn’t previously possible.
The Grand Award winner, featured on the 2022 GM Chevrolet Silverado and GMC Sierra, reportedly is the first all-composite leaf spring for light trucks. Produced by Mubea, a German tier 1 automotive and aviation supplier, using epoxy/prepreg layup and compression molding, this part reduces weight up to 75% vs. all-steel and 58% vs. hybrid steel/composite solutions, while doubling durability, eliminating corrosion, improving ride comfort, lowering NVH, and increasing payload. Fiberglass/epoxy prepreg is used to form a single leaf with a progressive spring rate that eliminates the shackle, shackle bushing, and helper leaves.
Featured on the 2022 Ford F-150 Lightning is a customizable, shielded high-voltage power distribution system that allows production of seven sets of subassemblies and up to 64 possible configurations from a single injection mold. It was produced by Yazaki North America with three different materials from DuPont (now products of Celanese). A flame-retardant 25%-glass/PBT (Crastin FR684) forms the injection molded internal assembly and terminal blocks and a silicone seal is overmolded directly onto a 30% glass/PBT (Crastin HR5339) cover. A unique shielding system uses stamped connection interfaces that reduce mass by two-thirds vs. cast products while maintaining electromagnetic shielding. Each individual component can be molded either open or closed, allowing for various accessory options and vehicle routing scenarios.
Two developments on the 2023 General Motors’ Cadillac Lyriq provide a lightweight, thermoplastic solution for thermal management systems of electric vehicles and are said to challenge the use of EPDM and TPV. Manufactured by Cooper Standard, one includes the use of its proprietary PlastiCool 2000 lightweight multi-layer tube construction. It is designed for glycol applications to 248 F/120 C such as cooling systems for internal-combustion engines, hybrid and battery electric systems, and is said to provide excellent chemical resistance plus 25% better permeation resistance and 60% lower weight than EPDM.
Meanwhile, Cooper Standard’s patented Ergo-Lock+ modular VDA connectors reportedly are flexible, offer visual and scannable latch verification, and reduce insertion forces by over 30%. The modularity of the system, manufactured with extrusion, molding, forming and automated assembly, permits hundreds of connector configurations to be produced from a standard set of molded subcomponents at lower total cost. The materials used for PlastiCool 2000 are PP from LyondellBasell and nylon 66 from DuPont while Ergo-Lock is made with DuPont’s nylon 612 (these nylons are now part of Celanese).
High-pressure oil-cooler gasket seals on the 2022 GM Chevrolet Silverado and GMC Sierra, appeared to be a first in that they were made of a new ethylene acrylic TPV that competes with fluoropolymers. Injection molded by Tier I Uchiyama (UMC) Marketing & Development America, the seals are made from UMC V7401 TPV developed jointly with DuPont.
Oil-cooler gaskets are small parts with important sealing functions between oil coolers and oil pumps in demanding engine environments. The new TPV was developed to eliminate leaks seen with fluorocarbon seals during temperature cycling. It reportedly offers superior low-temperature sealing and maintains good compression set and controlled oil swelling from -40 F/C to 302 F/150 C and 14 bar oil pressure. Gasket height also was increased to provide higher contact pressure and better sealing. Costs were reduced 66% and sustainability was increased since the thermoplastic material is recyclable.
Winner of the Process/Assembly/Enabling Technologies category, light guides on the Chevy Blazer use a new direct-exposure laser welding process.
A new process, direct-exposure laser welding, replaced hot-plate welding to meet customer styling requirements for the light guides of the 2022 Chevrolet Blazer. Injection molded from Covestro’s Makrolon LED 2245 000000 PC, tier 1 Magna Lighting replaced heated tools with scanning lasers that can weld opaque lens borders without need for more costly laser-transparent materials.
Clearance between internal components and weld ribs iss reduced and ribs can be heated very precisely. The design’s complex geometries reportedly could not have been produced with traditional welding processes; furthermore, scrap was reduced 40% to 50% and energy usage by 85% to 95%.
Another first is the use of a patented recycling process that allowed reuse of post-industrial bilaminate scrap comprising TPO skins attached to crosslinked PP foam in the same interior-trim applications for the 2020 Chevrolet Silverado and GMC Sierra. Tier 1 Inteva Products used scrap from its Inteather TPO/PP extruded and coextruded sheets, which was repelletized and re-extruded into Inteather Eco TPO sheets for vacuum forming and injection graining as well as press lamination and assembly. An additive package reportedly eliminates/binds/deactivates reactive residuals and trapped gases from the foam. This program reclaims 1.5 million lb of TPO annually, replacing 50% of prime TPO, reducing landfilled scrap by 93%, and lowering CO2 emissions and energy usage by 48% each.
Sustainability and the Circular Economy are both a challenge and an opportunity to flexible packaging producers. Recyclable pouches based on all-PE multilayer structures, utilizing new resins and perhaps techniques like MDO or biaxial orientation, appear to be major contenders against glass, metal, and multi-material film structures.
Plastics Recyclers of Europe believes that 'colorful’ future trends will weaken the image of PET as a recycled product.
New radar-based measurement technology enables processors to extrude higher-quality pipe with less material. With an automated closed-loop control system you’ll get more output and less scrap to significantly lower costs.
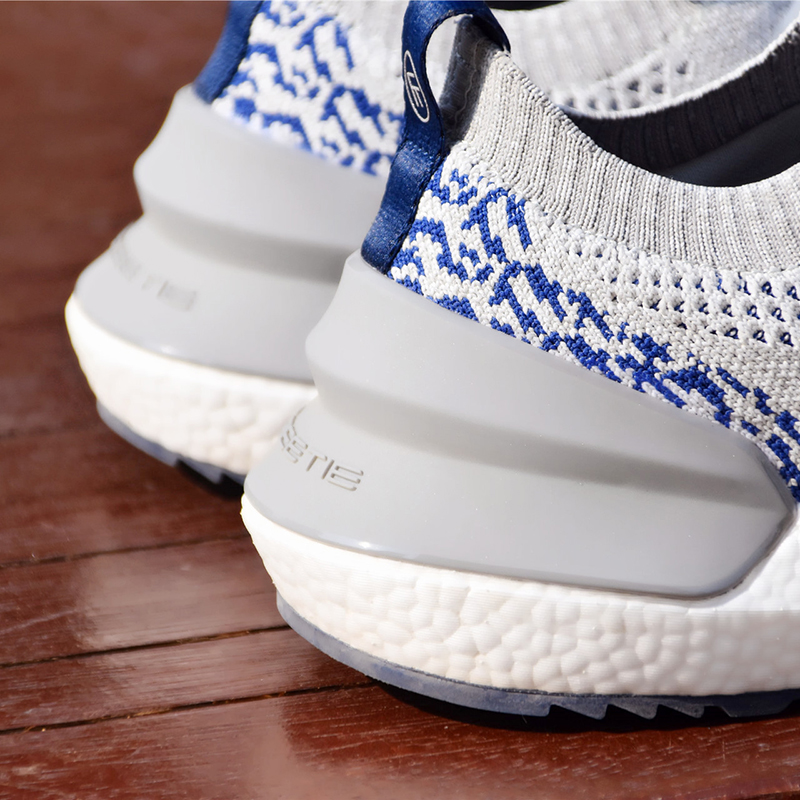
Uv Resistant Tpu © 2023 Gardner Business Media, Inc. Privacy Policy [Log On]